Rangeelo ⚹ Embroidered ⚹ Handwoven Woolen Shawl { 13 }
- Availability: Out Of Stock
- Made & Mkt by: Trajuva
- Product Code: 4052-DWL-13
- Weight: 450.00g
- Dimensions: 204.00cm x 91.00cm x 0.00cm
Rs.950
Don't miss out on the fun this winters by hiding yourself under those blankets...Put them aside & feel the wintry breeze on your face & let it ruffle your hair with its freshness...quietly...the warmth will sneak in, entangled with every thread of these woolen wraps... giving you a snuggly feeling in the midst of the city...
The typical dispatch time is 2-3 days; however, in special cases, it may take longer. Please refer to the product details section for specific timelines. Once dispatched, we will share the tracking details with you.
For returns, you can file a request within 24 hours of receiving the product. If the package is damaged, please make a video while unboxing and share images of the damaged item along with your return request.
Ever been to a music concert? …. Well the one that plays in the houses of Bhujodi is a wee bit different, not just in what you hear but also in the instruments that play. The musicians of Bhujodi play on … from morning to dusk, meditatively. Their orchestra constitutes of spin wheels for strings, wooden loom for beats, and for vocals there are chirping birds, sojourning the mud ledges for grains and water, offsprings giggling and playing pee-ka-boo across the courtyard, Mooing cow in the corner and almost certainly, filling the background will be either the folk tunes or the old bollywood melodies.
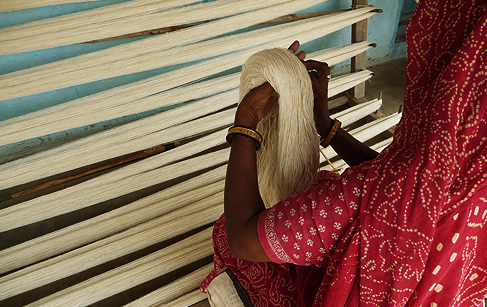
All of this manifesting into a concert, not just ears get accustomed to, but hands follow too. Meditatively weaving motifs out of a deeper conscience we call genetic inheritance. Each woven fabric carries with it, millions of such consciences, intertwined with the warp and the weft, closely put together to form the fabric of life.
Bhujodi, a 500 years old village in kutch is the mother to this need-fully evolved craft, shouldered by 200 of its weavers today. The craft is said to have evolved as a need to cover against weather, at the time barter system was practiced as a method of exchange. ‘Rabaris’ being the original nomads and cattle rearers provided wool, milk products and grains to the village and ‘Vankars’ took up to weaving cloth. While rearing cattle pretty much remained the same, the Vankars with an indigenous technique in hand had breakthroughs one after the other.
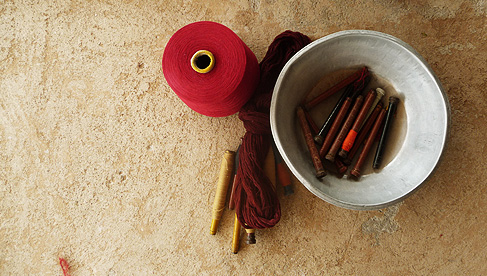
The basic structure of the loom remained the same, but it evolved to a more convenient model with time. The one in use today has the shuttle movement controlled by a foot-over pedal, as against the slow process of passing it through the warp manually. The fabric got finer with speed and variety of yarns available. The motifs however remained traditional and characteristic of communities. Like wheel, weaving is an invention that revolutionized the way we saw life there after, the basics holding valid till date.
While some wool from locally grown sheep is still used, they also procure silk from Bangalore, acrylic from Ludhiana, wool from Badmere and cotton from various places, to cater to the increasing demands. The fine cotton has enabled them to create more intricate and colorful designs. Such pieces may have 70 threads per square inch instead of the usual 24. Weaving of a piece may take days to months, depending upon the intricacy and newness of the design.
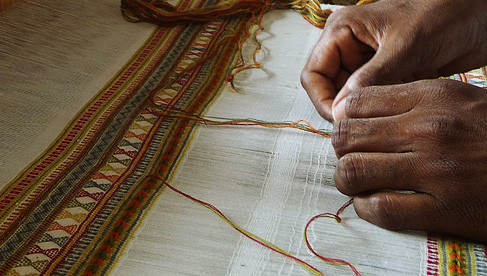
The yarn in its raw form is soft, breakable and capable of getting entangled easily. To get rid of these properties, a thin paste of wheat flour with water is boiled and the bunch of woolen strands is soaked in it. Soon after sun drying it in the fields, a layer of the paste covers the strands. These are then separated by combing them apart with a brush.
This bunch of strong strands is then taken inside the house, where several people are engaged in different stages of the weaving process. Some are busy cranking a machine that spins the thread onto a spindle, preparing the weft. A woman is working at high-speed to prepare the warp thread on a wooden frame called ‘chaukhta’. In the corner, a man is weaving on a shuttle loom. Vankaar Mosi Belji explained that, through the means of division of labor, it’s the men who sit on the loom as it needs a lot of stamina, while women take care of the auxiliary processes like making yarn on the charkha, laying it on the loom and adding value to the woven articles.
Inside his room, carpets, shawls, stoles and placemats were neatly piled. Some had bright colors others dark, and still others retained the natural color of the fibers. Many of them contained small round mirrors that were so naturally into the woven design.
Apart from Bhujodi, Vannora, Kota, Jamthara, Sarli, Bhuj, Kadarthi are other villages in Kutch region where weaving happens. Weaving as a process goes around the year apart from the rainy season, when work hits a lean because of practical reasons.
Not relying too much on today’s education system, the vankars train their future weavers from a very tender age. Growing around the traditional looms in the household, the kids learn by seeing, even before they develop conscience.
Craftsmen | |
Made by | Woven by: Shri Vankar Babubhai ladhubhai |
Returns and Exchange | |
Note | The products in this category are non refundable. Refund is only applicable in case of defect or damage. |
Material | |
Made of | Wool |
Instruction | |
Note | The products in this category is handmade. These might slightly differ from as seen on digital screen. |
Care | The product is hand woven; gentle hand-wash or dry clean is recommended. Reshape and flat dry while it is damp. |
Bhagalpur, is one of the oldest towns of Bihar, references to which can be found in Indian epics like Mahabharata and Ramayana, as the kingdom of ‘Ang..
Rs.9,000
Bhagalpur, is one of the oldest towns of Bihar, references to which can be found in Indian epics like Mahabharata and Ramayana, as the kingdom of ‘Ang..
Rs.22,000
Bhagalpur, is one of the oldest towns of Bihar, references to which can be found in Indian epics like Mahabharata and Ramayana, as the kingdom of ‘Ang..
Rs.11,500
Bhagalpur, is one of the oldest towns of Bihar, references to which can be found in Indian epics like Mahabharata and Ramayana, as the kingdom of ‘Ang..
Rs.15,500
Bhagalpur, is one of the oldest towns of Bihar, references to which can be found in Indian epics like Mahabharata and Ramayana, as the kingdom of ‘Ang..
Rs.11,500
Bhagalpur, is one of the oldest towns of Bihar, references to which can be found in Indian epics like Mahabharata and Ramayana, as the kingdom of ‘Ang..
Rs.8,900
Bhagalpur, is one of the oldest towns of Bihar, references to which can be found in Indian epics like Mahabharata and Ramayana, as the kingdom of ‘Ang..
Rs.9,000
Use Me Nothing Should Go Waste - Women on WingsOur belief in sustainability goes beyond products. We work with women who are in need to become em..
Rs.2,000
When Indra, the lord of rains, showed his wrath on the people of Vrindavan, with violent rains and thunder, lord Krishna lifted the Govardha..
Rs.16,900
The original inhabitants of the land, their imagination uninfluenced by any norms, they depend on nature for any inspiration. They carry forwar..
Rs.948
Indigo, spices, muslin and ivory – these were the items of luxury exported from India in the ancient times. Considered a noble craft, ivory ..
Rs.1,140
When Indra, the lord of rains, showed his wrath on the people of Vrindavan, with violent rains and thunder, lord Krishna lifted the Govardha..
Rs.0
Dating Dhurries Back In Time Flat-weave rugs are called dhurries in India. They have been woven for centuries, perhaps..
Rs.8,250
Gathering commences in the middle of deserted pavilions where velvet carpets adorn the Dessert lands & Manganiyars play folk music as a bugle for ..
Rs.512 Rs.1,025
Gathering commences in the middle of deserted pavilions where velvet carpets adorn the Dessert lands & Manganiyars play folk music as a bugle for ..
Rs.512 Rs.1,025
Gathering commences in the middle of deserted pavilions where velvet carpets adorn the Dessert lands & Manganiyars play folk music as a bugle for ..
Rs.512 Rs.1,025
Gathering commences in the middle of deserted pavilions where velvet carpets adorn the Dessert lands & Manganiyars play folk music as a bugle for ..
Rs.512 Rs.1,025
A familiar chatter swells in the air as feet chase the trail of a carelessly flying odhani in the by-lanes of Bhuj, spilling colors all over. While&nb..
Rs.3,070 Rs.3,412
A familiar chatter swells in the air as feet chase the trail of a carelessly flying odhani in the by-lanes of Bhuj, spilling colors all over. While&nb..
Rs.9,310 Rs.10,345
A familiar chatter swells in the air as feet chase the trail of a carelessly flying odhani in the by-lanes of Bhuj, spilling colors all over. While&nb..
Rs.3,460 Rs.3,845